In 3D mở ra nhiều cơ hội mới cho ngành điện gió
Nhiều chi tiết, bộ phận của những tuabin điện gió lớn (như mẫu Haliade-X của GE) được đúc tại một số xưởng ở Tây Ban Nha và Đức. Trong khi đó, nhiều xưởng đúc khác lại cách các trung tâm điện gió như Hoa Kỳ và châu Âu nửa vòng trái đất. Quy trình đúc truyền thống thường kéo dài vài tháng, đòi hỏi nhiều công đoạn lao động nặng và công nhân phải xử lý khối lượng lớn kim loại đun chảy để tạo ra sản phẩm cuối cùng. Tiếp theo, sản phẩm sẽ được chuyển đến nơi cần, có thể cách đó hàng nghìn cây số.
Vậy điều gì sẽ xảy ra nếu những xưởng đúc mới có thể sản xuất khuôn đúc cho các bộ phận tuabin bằng cách in một tệp dữ liệu trên máy in 3D cỡ lớn, đồng thời vị trí xưởng sẽ ở gần khách hàng hơn? Đây chính là ý tưởng mà nhóm nghiên cứu của GE Renewable Energy đã giới thiệu cho một đối tác thuộc ngành công nghiệp đúc trong chuyến thăm gần đây – theo Juan Paul Cilia, kỹ sư thiết kế cấp cao tại GE Renewable Energy.
Quá trình in 3D chi tiết vỏ động cơ tuabin gió. Ảnh: Voxeljet.
Theo Cơ quan Năng lượng Quốc tế (IEA), tổng công suất lắp đặt điện gió ngoài khơi trên thế giới dự kiến sẽ tăng gấp 3 lần vào năm 2025 và sẽ gấp 15 lần vào năm 2040, phần lớn nhờ vào chi phí sản xuất giảm, sự hỗ trợ của chính phủ và những tiến bộ công nghệ. GE cùng với Viện Nghiên cứu công nghệ đúc, composite và chế biến Fraunhofer IGCV – một trong những tổ chức nghiên cứu hàng đầu châu Âu và Voxeljet AG – công ty sản xuất máy in phun kết dính cát cỡ lớn – đang nỗ lực đưa một trong những tiến bộ nói trên ra thị trường. Cụ thể, họ đang thiết kế một máy in 3D phun kết dính cát lớn nhất thế giới để sản xuất các chi tiết, bộ phận cho tuabin gió ngoài khơi. Thiết bị này được gọi là Advance Casting Cell (ACC).
Công nghệ in phun kết dính có một số điểm tương đồng với máy in 3D kim loại dùng tia laser: đều sử dụng chùm tia sáng để nung chảy các lớp bột kim loại. Tuy nhiên, điểm khác biệt chính là in phun kết dính sử dụng chất kết dính để làm cho hỗn hợp cát dính chặt vào nhau, tương tự như cách thợ làm bánh dùng trứng để giúp bột bánh mềm dẻo. Bên cạnh đó, máy in phun kết dính còn có thể in nhanh hơn nhiều so với các máy in sử dụng tia laser đồng thời có thể sản xuất những chi tiết có kích thước lớn hơn.
Các thử nghiệm dự kiến sẽ được tiến hành vào đầu năm tới, trong khi đó nhóm nghiên cứu đã định hình ra một máy in 3D có khả năng sản xuất khuôn cho các bộ phận chính của tuabin có đường kính lên tới 9,5m và cao tới 4m. Thiết bị này có khả năng giúp loại bỏ một số công đoạn tốn thời gian nhất trong quy trình đúc truyền thống.
Cách thức hoạt động của máy in phun kết dính. Ảnh: Voxeljet.
Trong lần hợp tác này, GE sẽ cung cấp một số bí quyết kỹ thuật về tuabin và bản vẽ thiết kế kỹ thuật số của những chi tiết cần in. Trong khi đó, Fraunhofer IGCV sẽ tiến hành nghiên cứu và phát triển (R&D) để kết hợp các ý tưởng in mới và thử nghiệm. Cuối cùng, Voxeljet chịu trách nhiệm khâu thiết kế, phát triển cơ khí và chế tạo máy in nguyên mẫu cũng như thương mại hoá dòng máy in này. “Tôi không phải là kỹ sư. Tôi là nhà thiết kế công nghiệp” – Cilia nói. “Chúng tôi chỉ nêu ý tưởng, đặt các câu hỏi phù hợp và tò mò vừa đủ để thử xem liệu ý tưởng đó có khả thi hay không. Chúng tôi khuyến khích toàn bộ nhóm nghiên cứu tư duy khác biệt, đổi mới hơn, mạo hiểm hơn và hãy cứ thử nghiệm”.
Quy trình đúc các chi tiết cho một thiết bị công nghiệp lớn như tuabin Haliade-X thường bắt đầu bằng việc chế tạo một mô hình gỗ. Công đoạn này mất từ 10-12 tuần. Sau đó, công nhân sẽ ép mô hình vào hỗn hợp cát kết dính bằng nhựa thông và tạo hình ảnh âm bản của chi tiết cần đúc. Tất cả các khâu nói trên có thể kéo dài tới hàng tháng.
Trong khi đó, in 3D cho phép bỏ qua công đoạn tạo mô hình – khâu tốn thời gian nhất trong quá trình đúc – và in trực tiếp khuôn trên máy in phun kết dính bằng một tệp dữ liệu. Kết quả là, vật đúc có thể sẵn sàng xuất xưởng chỉ trong bốn tuần. “Chúng tôi đang đề xuất tạo những khuôn đúc này theo cách tự động hơn, không theo khuôn mẫu” – Cilia chia sẻ.
Cách tiếp cận này có nhiều lợi ích tiềm năng. Không chỉ đẩy nhanh quá trình đúc, nó còn có thể giảm chi phí đồng thời hỗ trợ ngành công nghiệp đúc phát triển bền vững hơn bằng cách giảm thiểu tác động môi trường của ngành này. Dennis Lessner – Trưởng nhóm Sáng kiến Chiến lược, bộ phận Chuỗi Cung ứng của công ty Offshore Wind thuộc GE Renewable Energy cho hay: “Điều quan trọng là phải tạo ra giá trị tại địa phương vì nó có ý nghĩa rất lớn khi xin phê duyệt các dự án điện gió.” Cụ thể hơn: “Các quốc gia không chỉ muốn sản xuất điện sạch hơn mà còn muốn nhìn thấy lợi ích của ngành này. Với công nghệ in 3D mới, chúng tôi có thể tăng khả năng cạnh tranh tại những nơi cần tới các chi tiết đúc cũng như có thể sản xuất nội địa và giúp ngành công nghiệp nội địa hưởng lợi từ sự bùng nổ đang diễn ra trong lĩnh vực năng lượng tái tạo”.
Không chỉ thế, in 3D còn có thể giúp kỹ sư sản xuất những vật đúc lớn hơn, nhẹ hơn với hình dạng kết cấu phức tạp mà sẽ rất khó hoặc không thể đúc truyền thống bằng mô hình gỗ. Đổi lại, điều này giúp nhà thiết kế có thể xây dựng các tuabin cao hơn, có công suất lớn hơn. Lessner chia sẻ: “Với công nghệ truyền thống, ta chạm đến một ngưỡng nhất định khi các thiết kế lớn hơn quá to và nặng nên không thể sản xuất được.”
Cilia bổ sung thêm: “Cánh cửa đang rộng mở. Trước đây, rất nhiều ý tưởng của các nhóm kỹ sư từng không thể thực hiện do nhiều hạn chế trong sản xuất. Nhưng giờ đây, họ có thể tự do thiết kế – theo đúng nghĩa đen.”
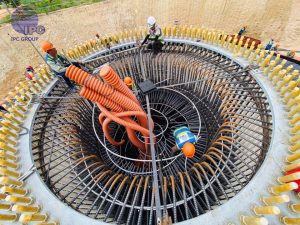
Khuôn móng tuabin điện gió dự án Yangtrung, Chơ Long (Gia Lai)